We visited the Lung Tam Co-operative where Hemp is woven on traditional looms. Batik is used to create the intricate patterns that the group are recognised by. Having collected some pieces myself of traditional Hmong textiles in Vietnam and Laos, I was delighted to witness their creative skills. A 95 year old lady meticulously draws her patterns in hot wax with the steadiness of hand I could only wish to have myself.
Read Moreweaving
Know Disaster No Disaster - Wall graffiti. Thamel. Kathmandu
After our decent from Nagarkot, we had half a day left in Thamel, Kathmandu - time was of the essence… I have been very drawn to the fabrics here in Nepal. Similar to my paper addiction, I also have a fabric addiction, it has developed initially from interior design to now incorporating fabric into my artwork. There is something very different to the feel of Nepalese fabric so I did a bit of hunting and found a contact online, coincidently just down the road from our hotel. A few what’s app messages later and we met Ajay who has a weaving factory. He produces modern raw-silk fabrics using traditional methods and more recently using eco-dying and we were going to visit where the magic happens.
Firstly Ajay took us to his premises in Thamel - a small, modern clothes shop which had just opened for business that very morning. The rooms behind were where the clothes were made before being exported to select countries around the world. Customers can either buy the fabric or the garments.
The Nepal Handloom Silk Industry is the first and only company in Nepal to manufacture and export hand-woven raw silk fabrics and garments. It is currently a 2nd generation business run by Ajay who took over from his father.
The room where the handmade fabrics were stored took my breath away. What is different is that many are created using natural dyes and woven in unique combinations and thicknesses on a hand-loom. I have never seen or felt silk, linen and wool worked like this. These fabrics do not have the conventional weight, look or feel of silk.
Nepal Handwoven Raw-Silk
Nepal Handwoven Linen
Pattern matching for a Japanese client.
After a while we jumped into a car and went over to Ajay’s factory - some bungalows behind his home.
Ajay’s business - ‘Nepal Handloom Silk Industry - uses an aged and traditional style of handloom weaving, which creates fabric with a luxurious feel. The fabrics are woven on an old and long-established Foot–Treadle Floor Loom. Weaving is done by intersecting the longitudinal threads, the warp, i.e. “that which is thrown across”, with the transverse threads, the weft, i.e. “that which is woven” ‘- as explained on his website http://www.nhsi.com.np
In the first building are the foot-treadle floor looms and the spinning wheels. The sound of the looms is magical. The weft takes many days to set up.
The warp is spun the onto spools and they go into the shuttles. The shuttles weave together the 2 layers of weft. The tension determines the weight and feel of the raw-silk.
Spinning the spools for the shuttle
In the second bungalow are some enormous pieces of machinery that are dedicated to the semi-automated weft alignment. The weft is set up for the desired meterage then transferred on a large roller to the loom where is it fed through all in perfect alignment. They do not make the weft, the thread is bought locally. This saves some time setting up the foot-treadle floor loom, especially with large lengths of fabric.
The roll of weft can allow around 20 - 40 meters of fabric to be woven,
Nepal Handloom Silk Industry first started dealing in Linens in the year 2005. Linen yarns are imported from China and India, then all the manufacturing process is done in Nepal. Like the process of manufacturing Handloom Silk and Pashmina, they use the old Foot–Treadle Floor Loom for weaving Linen fabrics.
The sad fact is that there is a decline in weavers. It is an artisan job but has never been well paid. Ajay is doing his best to raise the profile of weaving but youngsters are not really interested in this career choice. He has a small but talented team which I hope he can build on in the future. It would be a shame to lose this craftsmanship.
Ajay loves experimenting with the different weaving combinations of the raw silk or linen. His natural creations are beautiful and unique.
2 colourway raw-silk and avocado dyed linen.
Ajay has begun exploring eco-dying. Indigo - deep blue, avocado stones - pink, pomegranate - green/yellow, marigold - yellow/ orange and madder - vivid red with beautiful results. Only relatively small pieces can be dyed at a time mainly to ensure continuity within one garment.
Ajay has begun growing some of the relative plants in his garden - some with mixed success. Patience is required as it can take up to three years for a plant to yield any fruit. The monkeys from the nearby temple also pose a future threat to the success of the fruit supply.
After a cup of tea we returned to the office to collect a beautiful selection of raw silks that shall be put to good use back in the UK.
A few of the raw silks coming home with me
What a wonderful, spontaneous experience. Thank you Ajay!!
Farewell to the huge, beautiful mountain range and a country filled with beautiful people. How can we not return.
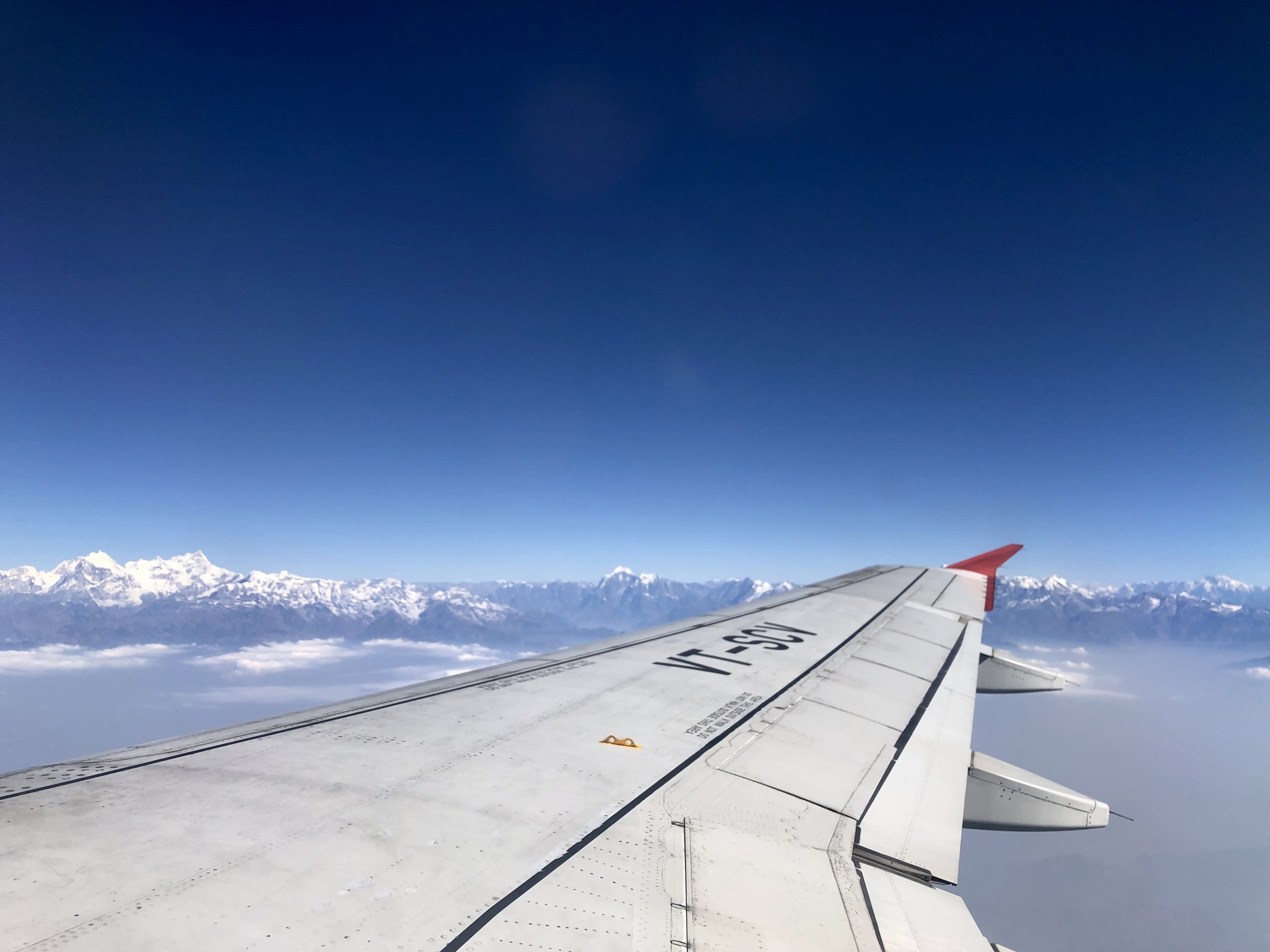
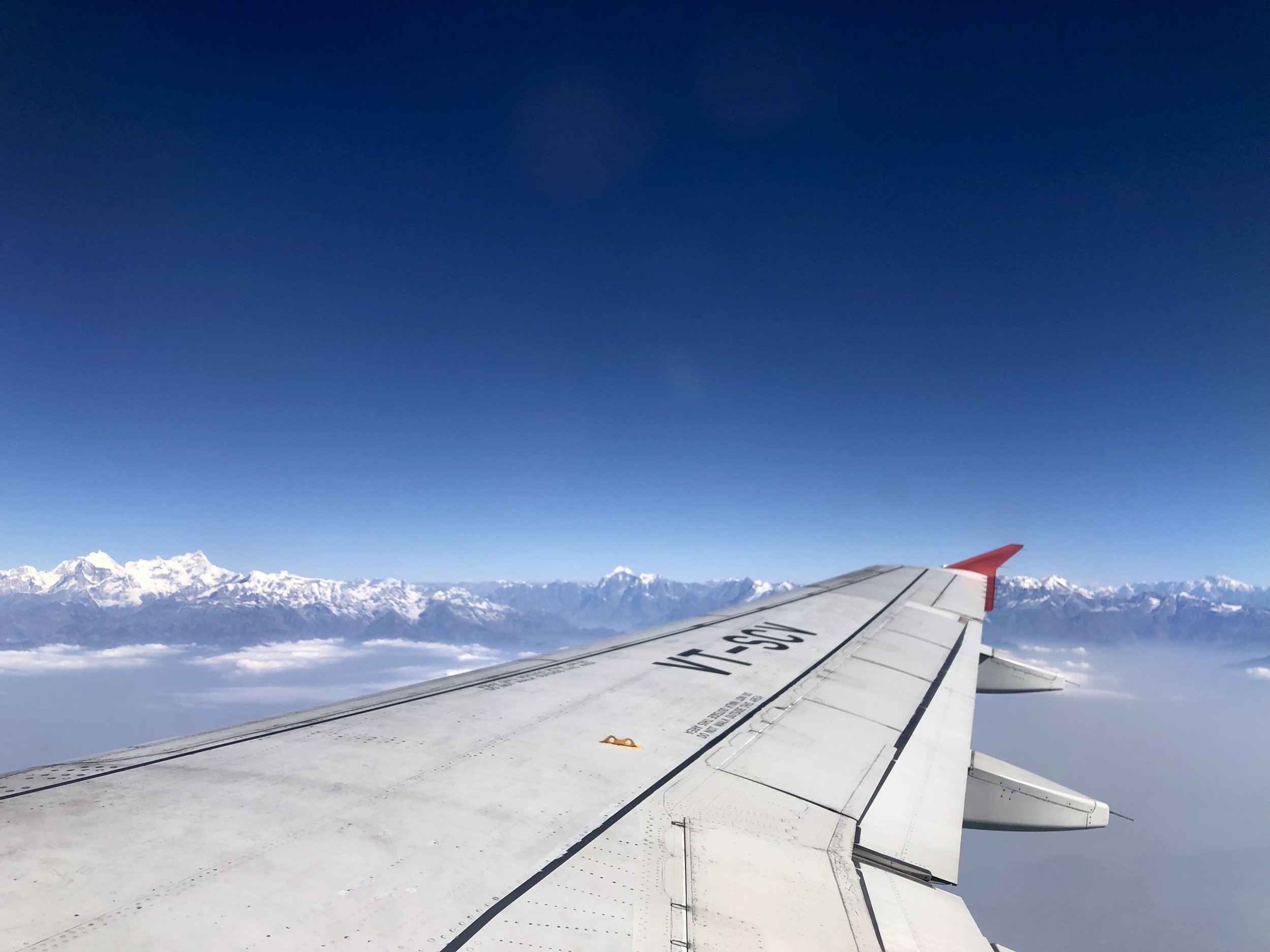
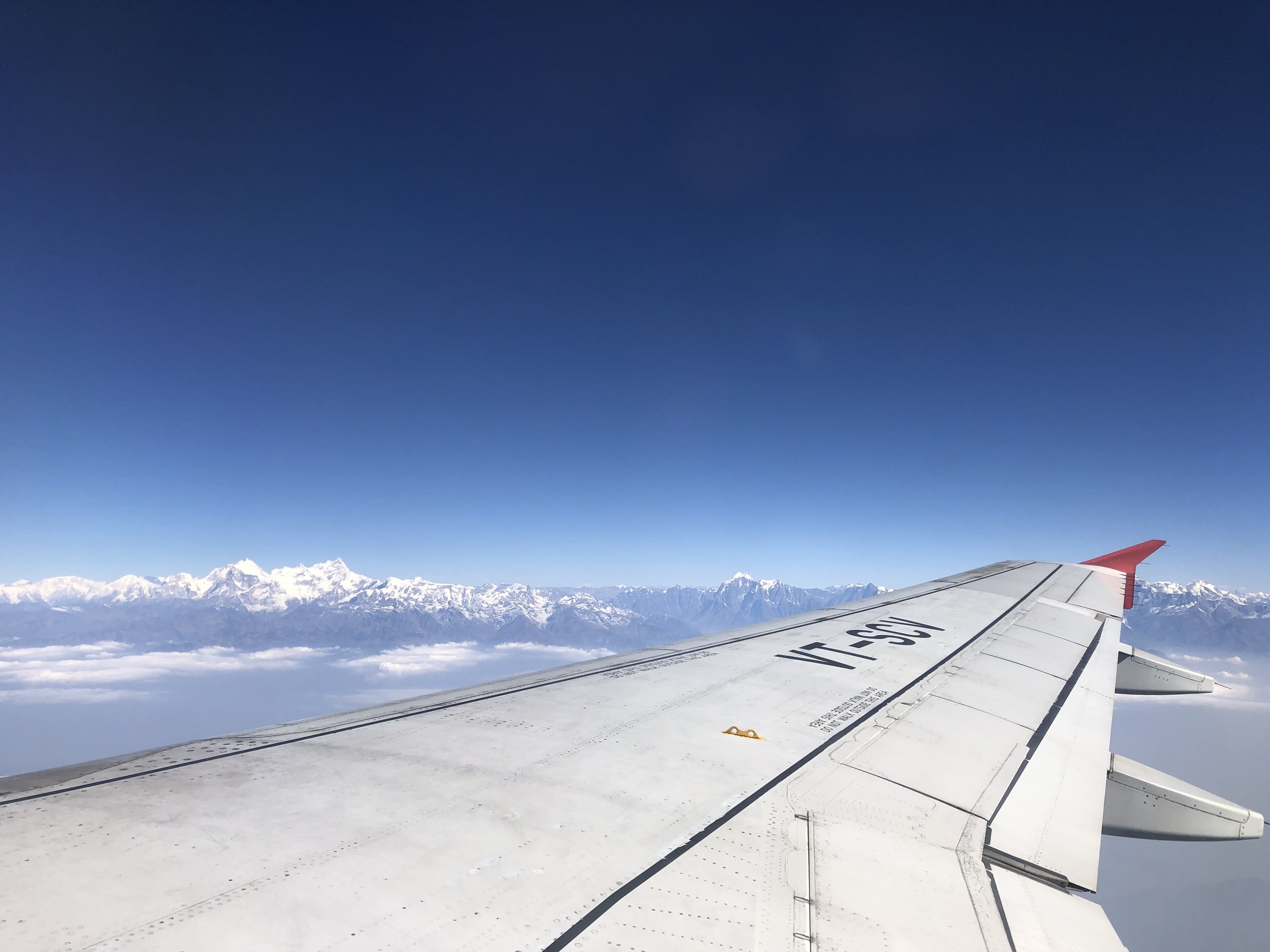
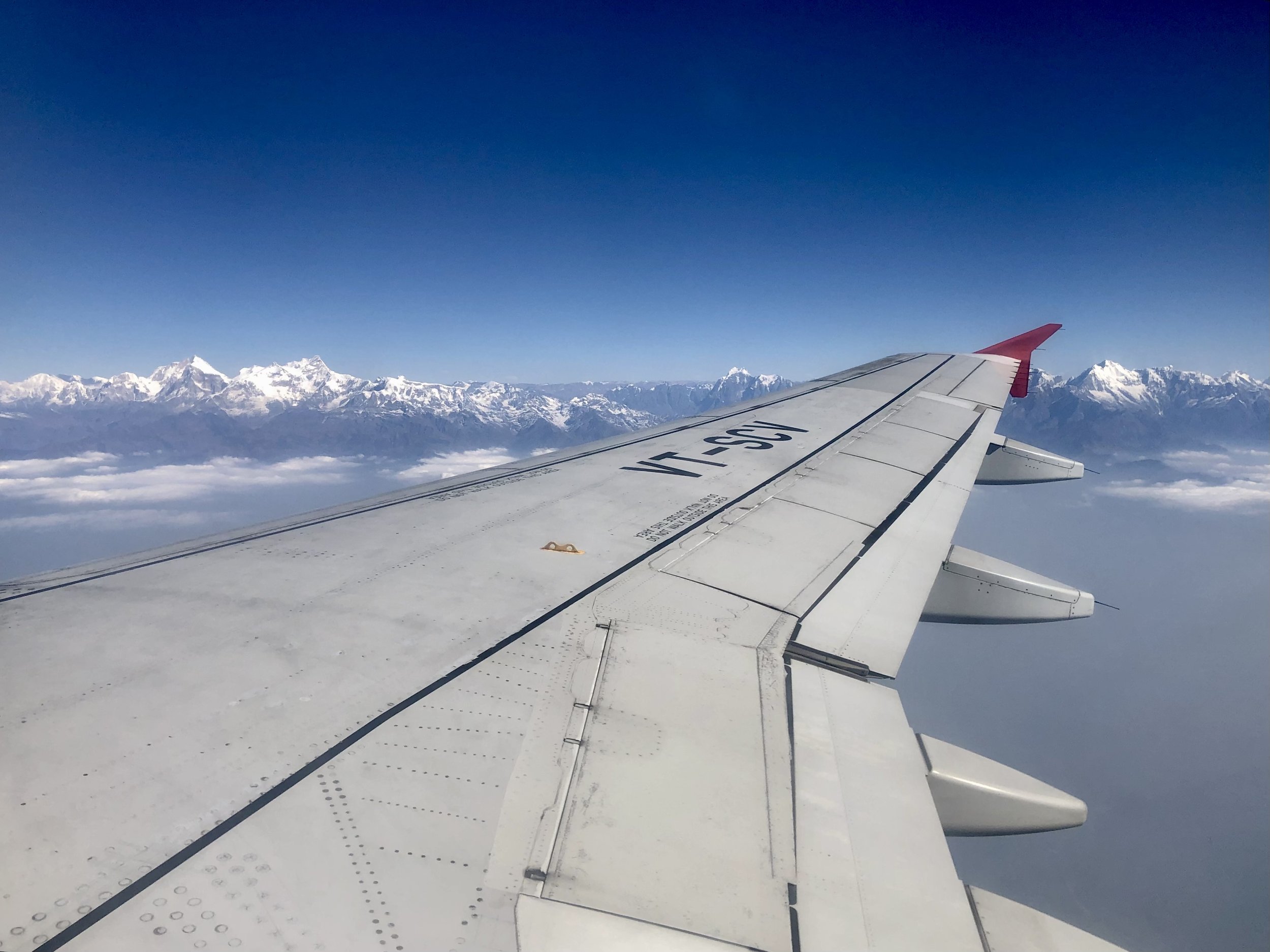
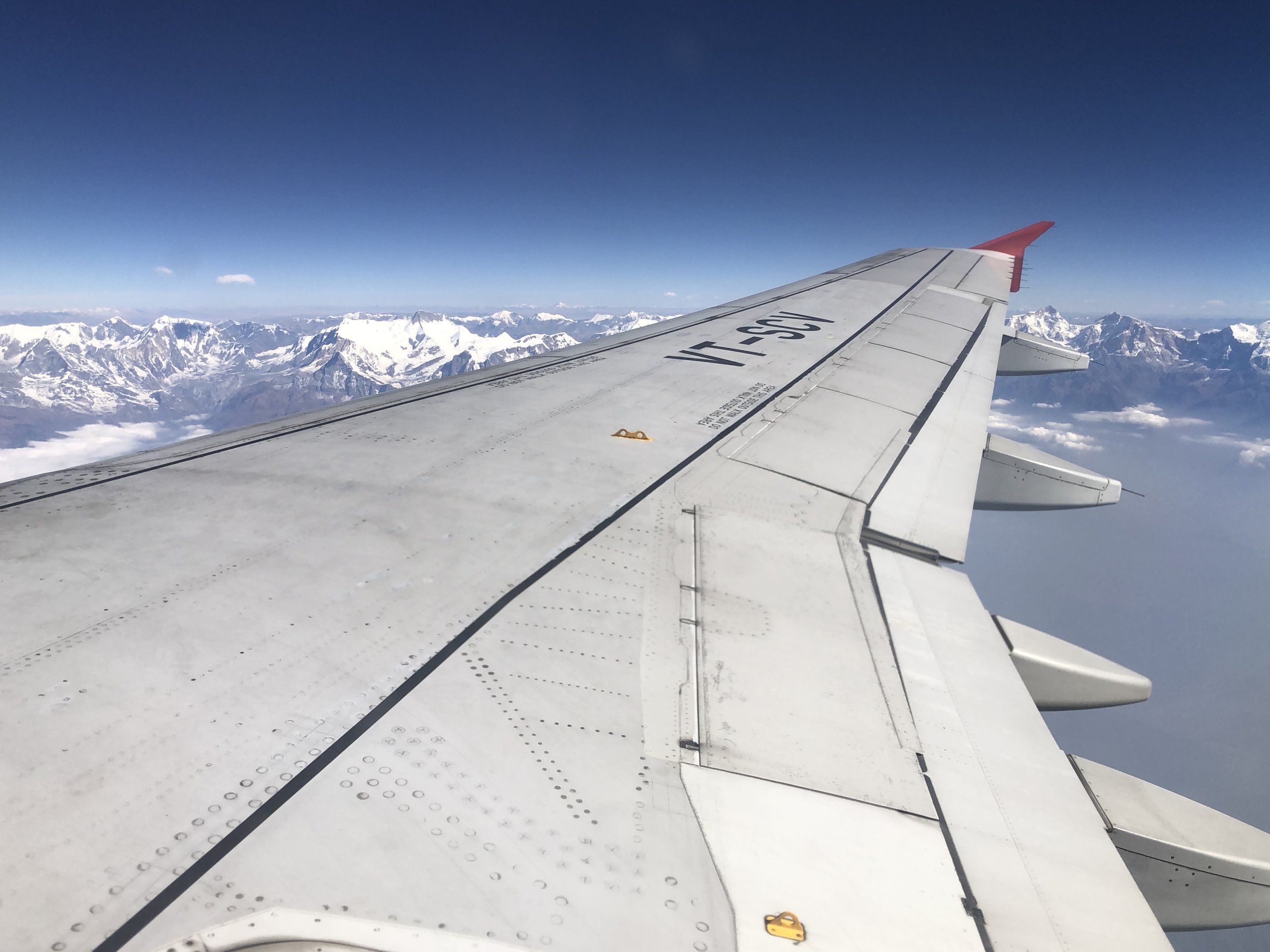
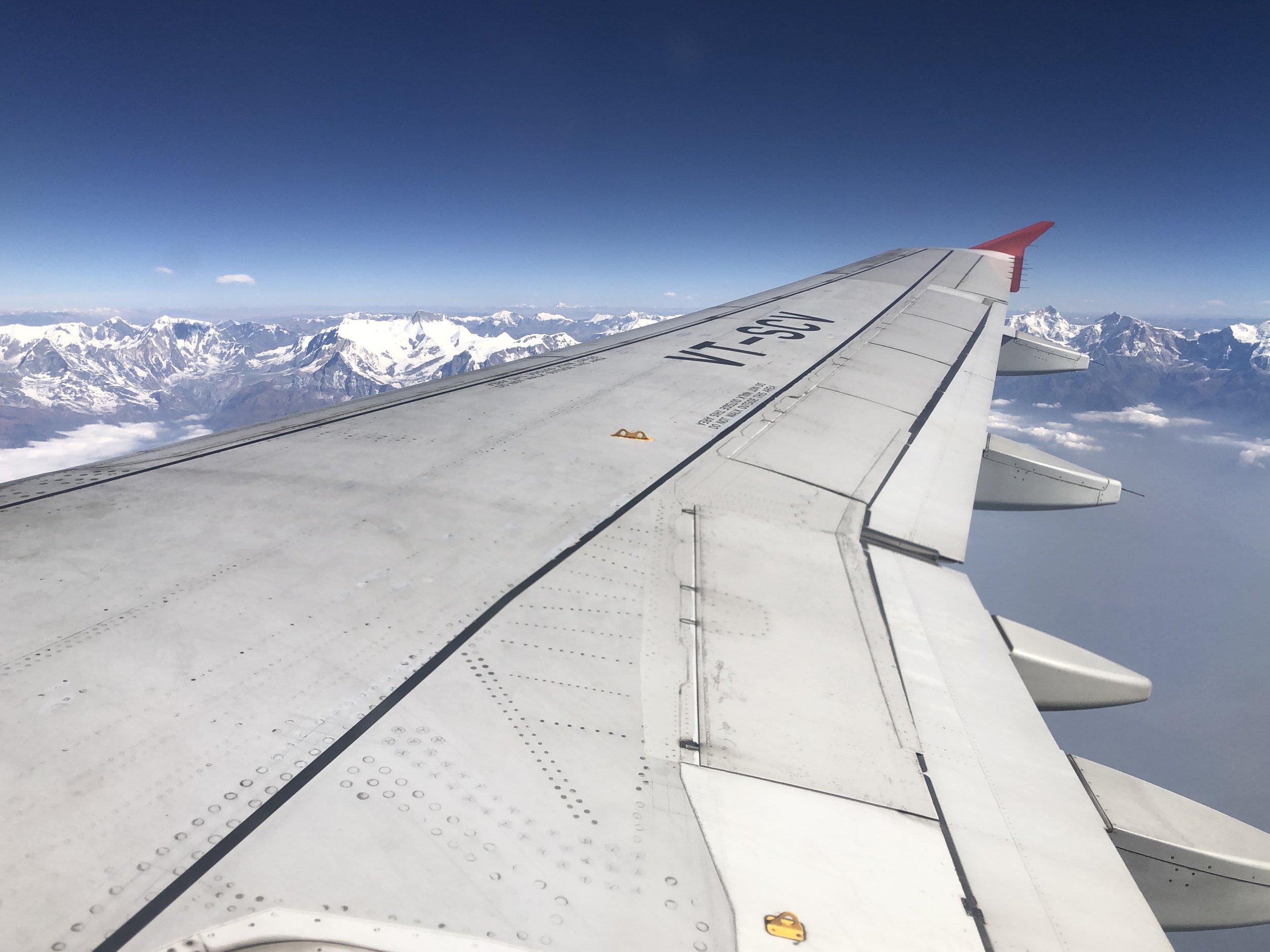
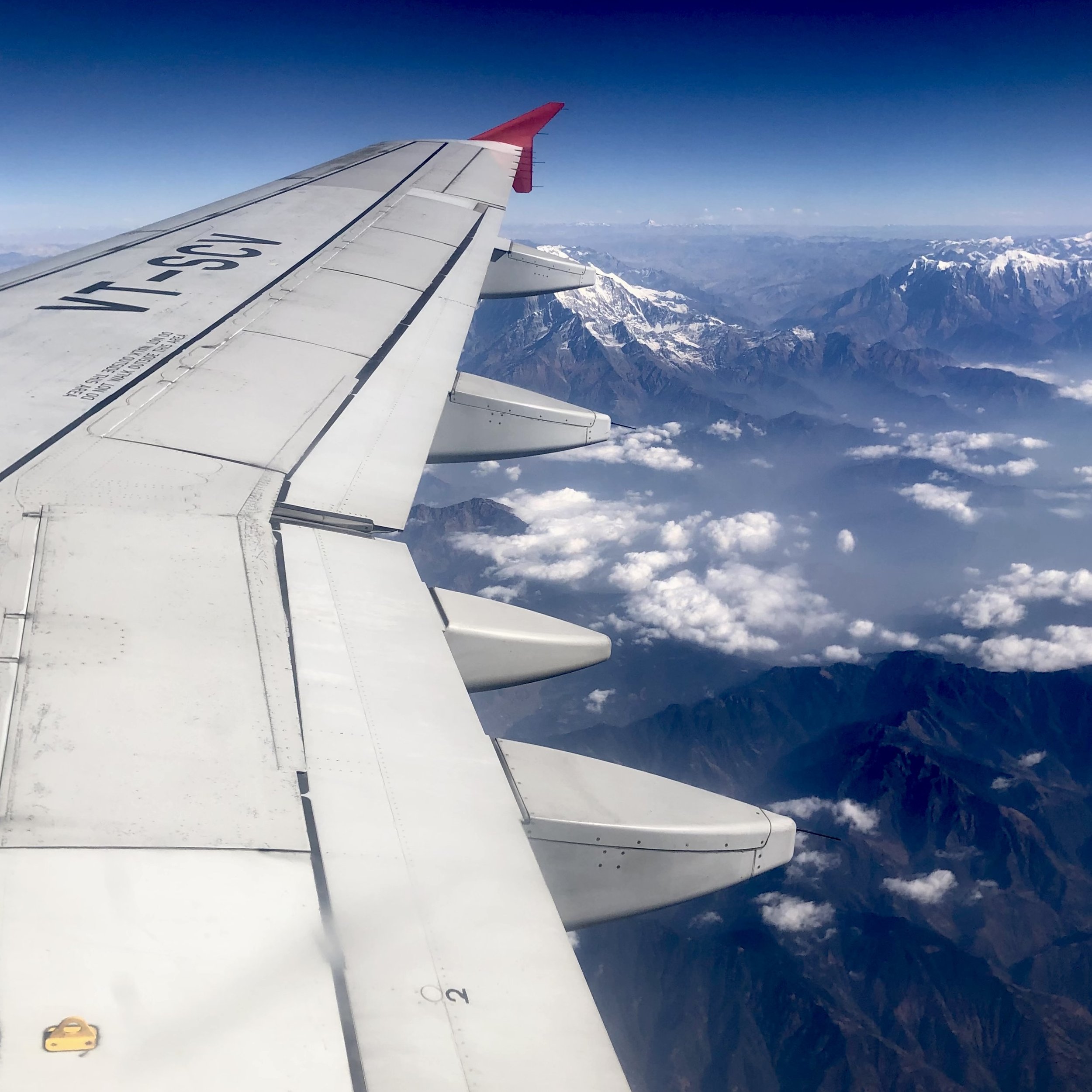
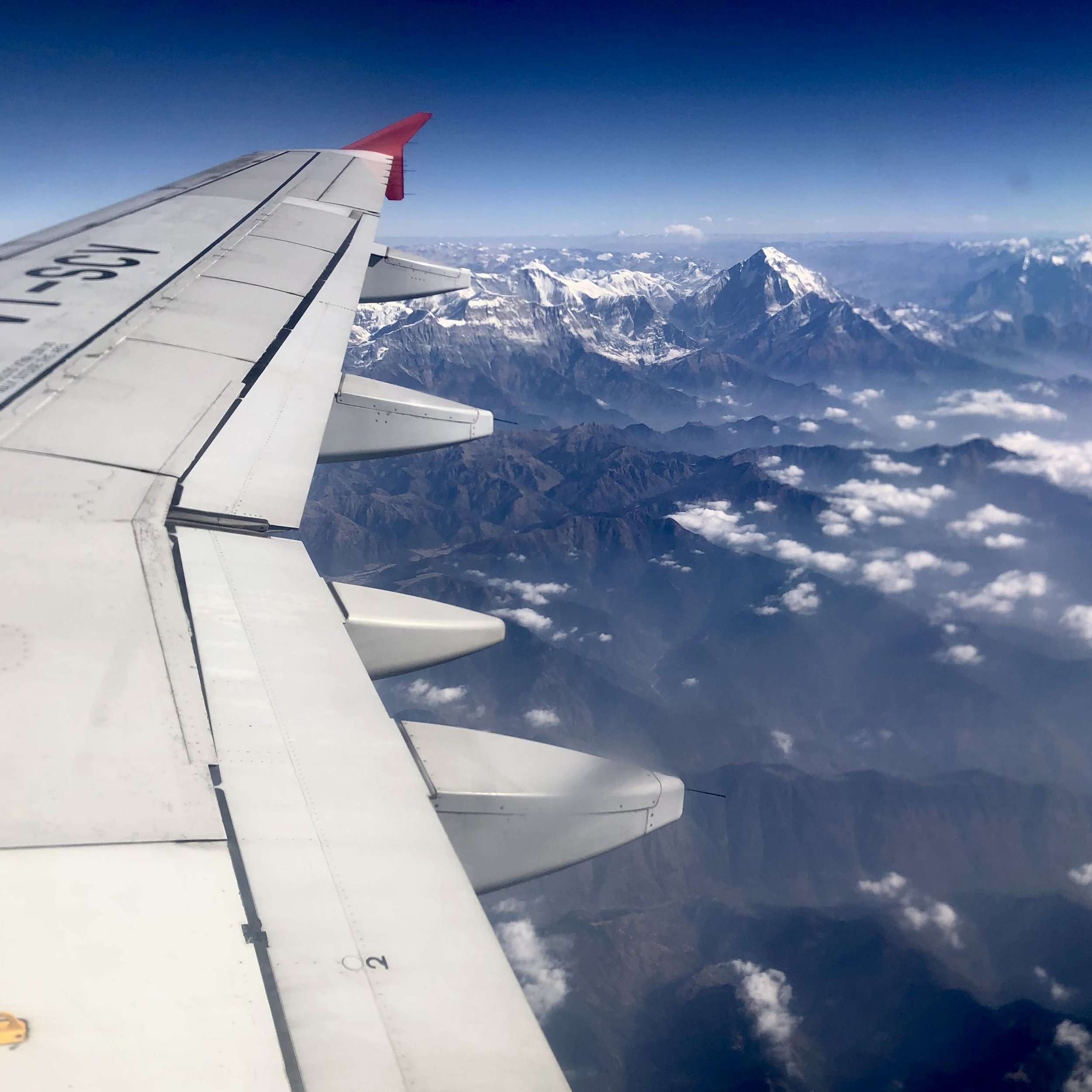
So its back to India and on to Chandigarh in the Punjab.